Assegnare a dei professionisti la costruzione delle schede elettroniche che servono al tuo business è come affidare a terzi il cuore pulsante della tua azienda, per questo ogni cliente che Eurek accoglie diventa inevitabilmente parte della famiglia: stima e fiducia reciproca sono gli ingredienti principali per poter cominciare a progettare e costruire i tuoi sistemi elettronici.
Flessibilità, rapidità, comunicazione e attenzione al cliente sono i pilastri che hanno reso Eurek un partner affidabile che prende a cuore il tuo progetto e lo fa diventare la sua nuova mission. Tutte le fasi necessarie per la creazione della tua scheda elettronica vengono svolte non solo con l’obiettivo di compiere il proprio lavoro di progettazione, costruzione, prototipazione ecc., ma soprattutto con il focus verso l’utente finale che si ritroverà ad interfacciarsi con il prodotto: per questo ci interessa capire ed entrare a far parte del tuo settore.
Operare con flessibilità ci permette di accogliere qualsiasi richiesta – anche quelle che possono rappresentare nuove sfide per Eurek – come costruire da 3 schede a 3000, progettare e costruire internamente, costruire internamente ciò che è stato progettato esternamente, progettare internamente e non costruire. In questo articolo, puoi scoprire come opera Eurek per la costruzione delle schede elettroniche.
Indice dei contenuti
La fase preliminare
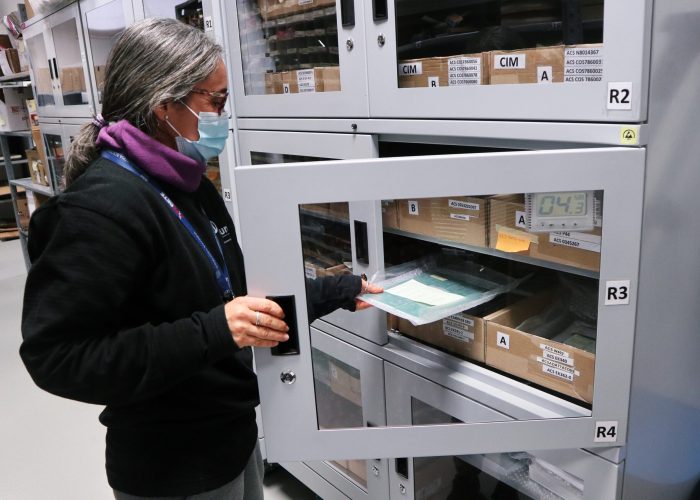
Prima di procedere con la costruzione delle schede è necessario avere a disposizione un progetto chiaro e studiato nei minimi dettagli per rendere più efficiente l’intero processo produttivo, ridurre i tempi di consegna e migliorare la qualità del prodotto. Questa fase si svolge in modo naturale tra i diversi reparti Eurek, ma se il progetto viene fornito dal cliente è necessario che vengano rispettati dei requisiti standard affinché la fase di produzione possa essere svolta in modo snello. In questi casi la flessibilità di Eurek incontra anche particolari richieste come l’utilizzo di una marca precisa di componenti o l’utilizzo di materiali forniti direttamente dal cliente.
Quando arriva la distinta, dal magazzino vengono preparati tutti i componenti elencati e necessari per la produzione del lotto di schede elettroniche. Questa fase è molto importante e rispetta i valori di rapidità e comunicazione che vigono tra i diversi reparti: infatti, il magazzino è organizzato secondo un ordine preciso, uno schema lineare, che consente di trovare facilmente i componenti e di prepararli con ordine e precisione.
L’organizzazione del magazzino è un elemento di fondamentale importanza se si vuole operare in un’ottica di Lean Production, non solo nella fase preparatoria dei componenti, ma anche nel controllo continuo dello stock disponibile e nell’acquisto tempestivo dei pezzi mancanti, nel ripristino di circuiti stampati e dei componenti attraverso il forno di Baking e nell’acquisto di nuove componenti.
Per garantire rapidità e affidabilità, è necessario che vi sia una chiara idea della tipologia di montaggio della scheda elettronica: la scelta può ricadere nell’utilizzo di componenti SMT (Surface Mount Technology) o PTH (Pin Through Hole) o, in particolari casi, possono essere montati i componenti sia SMT sia PTH.
Nel caso della tecnologia SMT è possibile assemblare i vari componenti sul circuito stampato in modo automatico, nel caso della tecnologia PTH il montaggio avviene manualmente sfruttando dei fori presenti sul circuito. Ci sono diverse situazioni in cui le schede elettroniche vengono montate con un mix delle due tecnologie: questo metodo si rivela infatti utile in presenza di componenti particolari o di notevoli dimensioni, tali da richiedere l’attività dell’uomo.
Componenti SMT
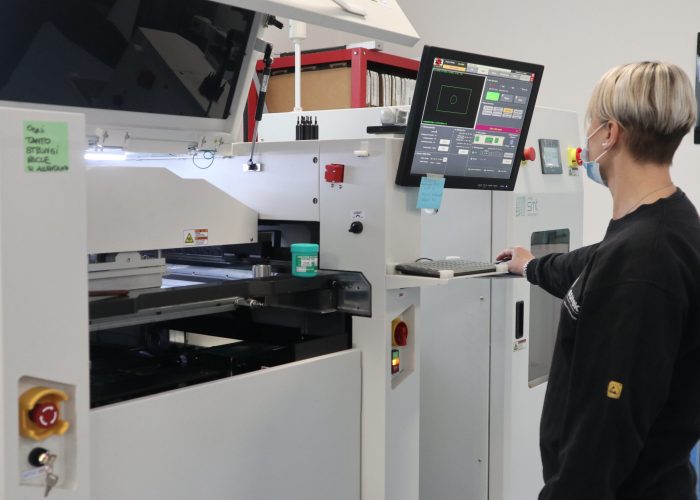
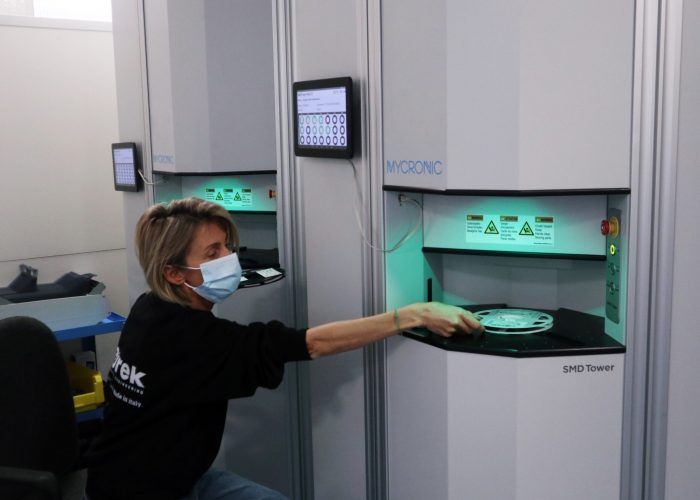
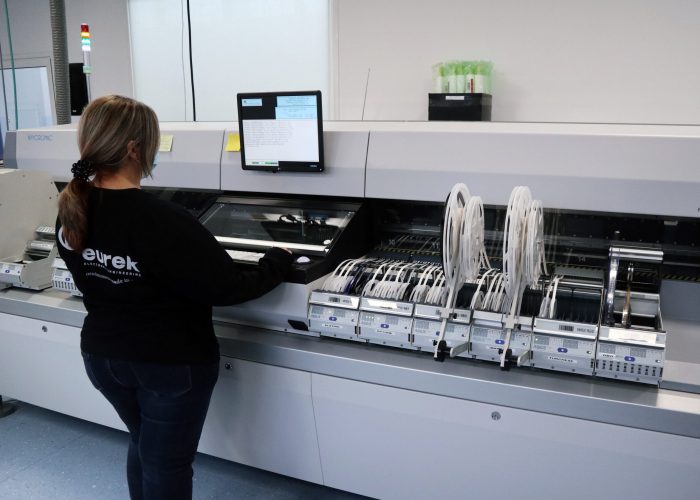
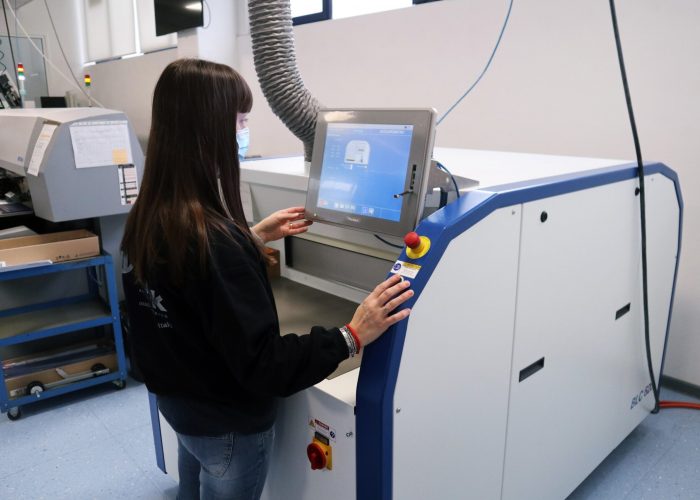
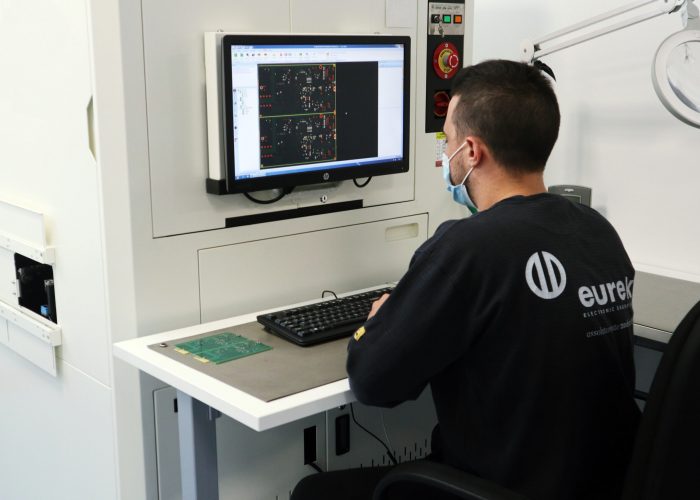
Il montaggio dei componenti SMT avviene in modo automatico, risultando ideale in quelle situazioni in cui vi è l’esigenza di montare tanti componenti su schede di dimensioni ridotte ma dalle prestazioni potenti, come le schede elettroniche dei cellulari, ad esempio.
All’interno del reparto SMT di Eurek è presente un magazzino automatico che può contenere fino a 2000 unità di componenti SMT in bobina, e che è in grado di selezionare in automatico il materiale necessario per il montaggio. Questa innovazione consente di snellire ulteriormente il montaggio dei componenti SMT, facendoli uscire in maniera automatizzata e rendendoli disponibili per la macchina pick and place.
In questa modalità di montaggio il circuito stampato viene immesso nella macchina serigrafica in cui una lamina sottilissima deposita dello stagno nei punti in cui dovranno essere inseriti i componenti. La fase successiva vede come protagonista la macchina Pick&Place adibita al prelievo e al posizionamento dei diversi componenti nel punto giusto del circuito: lavora autonomamente prelevando il componente necessario dalle diverse bobine su cui si trovano i pezzi da assemblare alla scheda elettronica.
Dopo il posizionamento dei componenti è necessario che vengano saldati per non rischiare distacchi dal circuito. La saldatura può essere effettuata per mezzo di una macchina vapour-phase, una tecnologia più recente che utilizza un liquido che raggiunge anche 230°C, trasformandosi di fatto in un vapore in grado di saldare la scheda elettronica, o un forno a infrarossi, più tradizionale che salda per mezzo del principio dell’aria. In entrambi i casi, la saldatura avviene per mezzo di shock termici differenti a seconda dei componenti da saldare.
Al termine di questa fase, se il prodotto necessita di ulteriori componenti che non possono essere assemblati in modo automatico, si passa al reparto PTH, altrimenti può passare alla fase di controllo o quella di collaudo.
La qualità del montaggio dei componenti sulle schede viene verificata tramite ispezione ottica con la macchina AOI (Automatic Optical Inspection) che in modo automatico analizza ogni pezzo montato sulla base, scansiona la scheda e verifica la presenza del componente e della polarità. Le immagini catturate dalla macchina vengono poi confrontate con il progetto iniziale ed eventuali anomalie segnalate in modo automatico.
Componenti PTH
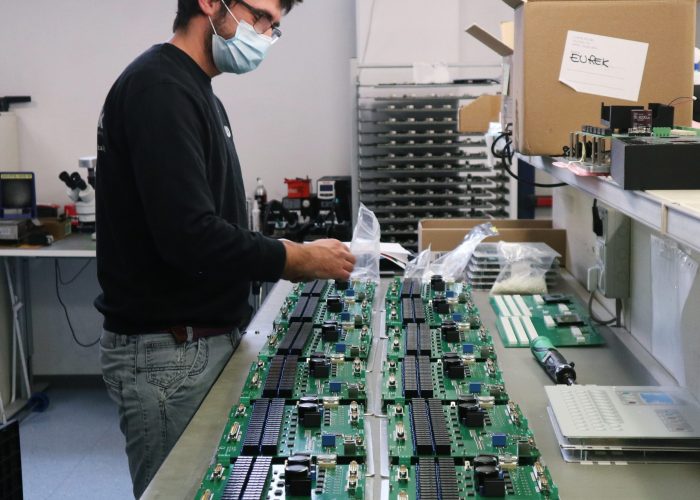
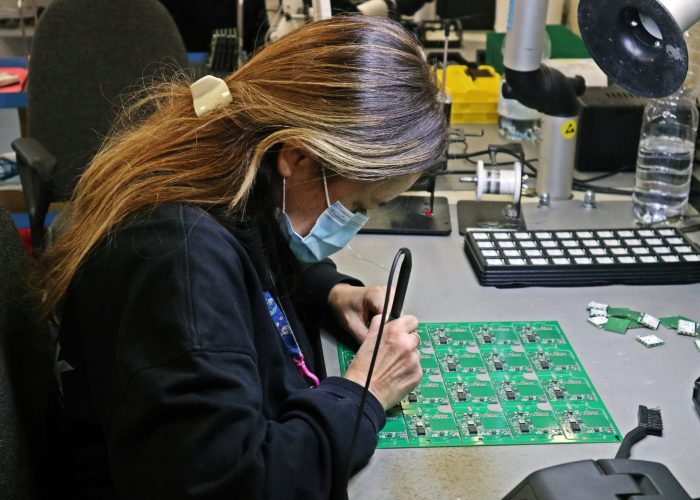
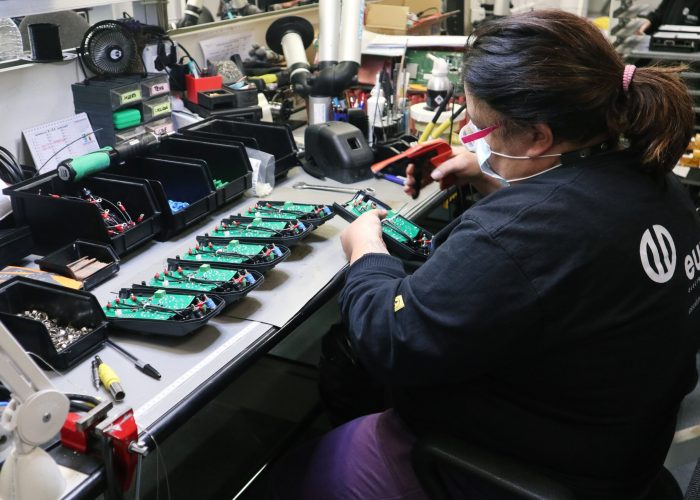
SMT e PTH sono tecnologie differenti ma che ancora convivono: spesso vengono utilizzati componenti PTH perché non si trova l’equivalente componente SMT, per scelte economiche o tecniche del progettista o perché è necessario combinare il montaggio di componenti SMT con quelli PTH.
Il montaggio PTH è una tecnica tradizionale utilizzata ancora oggi per quei componenti che non possono essere montati dalla pick and place, come i componenti grandi, e che necessitano di essere fatti passare dal lato A al lato B, attraverso un foro passante.
Per quanto riguarda la saldatura vi sono alcune sostanziali differenze sulle modalità, ad esempio, per la scheda SMT montata solo sul lato A la saldatura sarà effettuata a onda, se il montaggio avviene prima in SMT e poi in PTH la saldatura verrà effettuata a mano con un saldatore capace di raggiungere i 400°, se il montaggio viene effettuato solo da un lato e con tecnologia PTH la saldatura verrà effettuata a onda in modo automatico su un carrello in cui sono disposti più pezzi.
Prima di procedere con la saldatura viene generalmente spruzzato sul lato B uno spray flussante fondamentale per preparare la scheda che verrà poi preriscaldata a 270° per diventare chimicamente pronta per essere saldata. Dopodiché, la scheda viene fatta passare sopra a un’onda di stagno che “accarezza” la scheda nel lato B e ne salda i componenti.
Una volta ultimato il passaggio la scheda viene rimandata al reparto PTH per effettuare, se necessario, una rifinitura manuale della saldatura, verificare che non ci siano corti tra i pin e ricevere un’accurata pulizia prima di venire imballata e spedita.
Nel caso di schede elettroniche complesse, realizzate con componenti SMT o PTH, il controllo può essere effettuato mediante appositi macchinari per l’ispezione a raggi X che effettua una “radiografia” della scheda elettronica per visualizzare le caratteristiche dei componenti controllare la quantità di pasta saldante e verificarne il corretto apporto.
In conclusione…
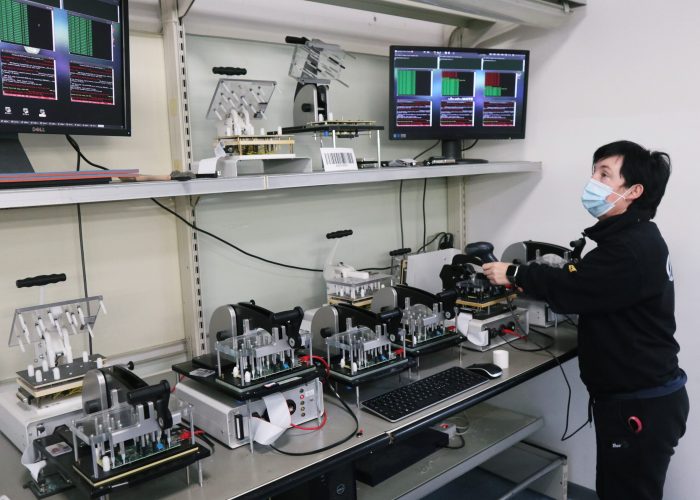
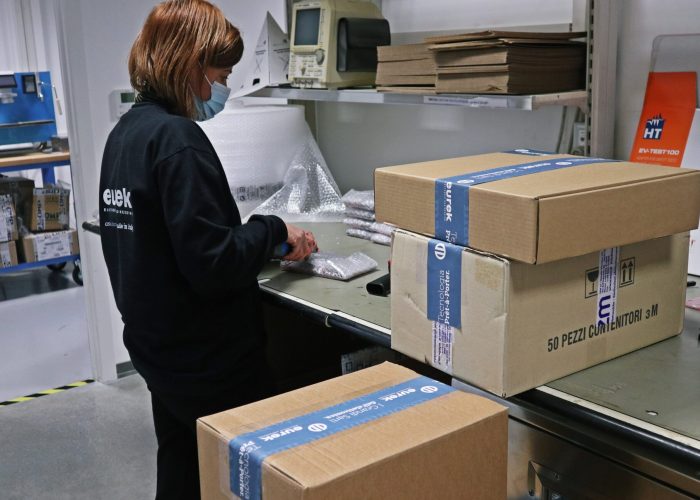
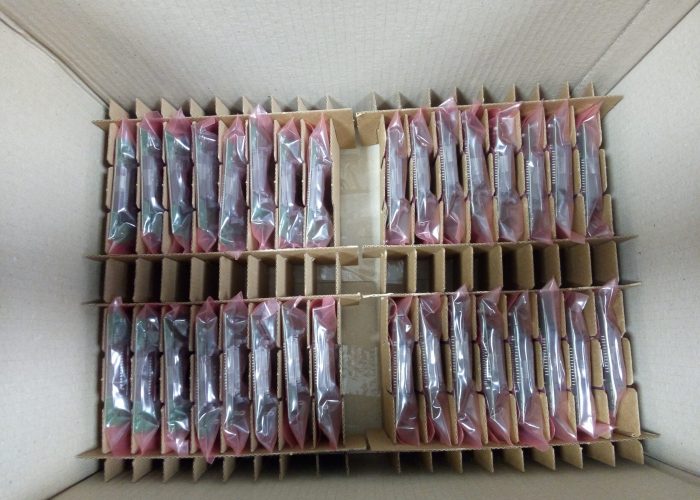
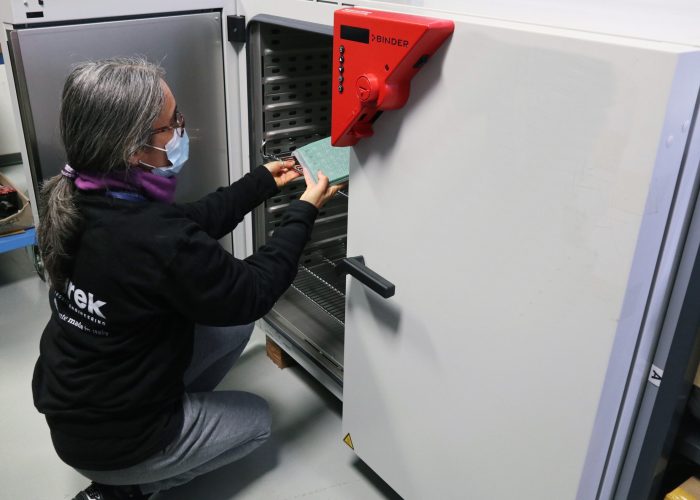
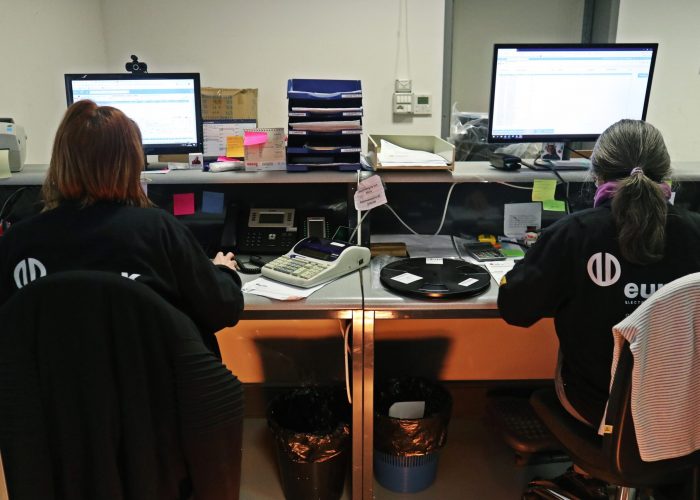
Dopo la fase di controllo il prodotto è pronto per essere spedito, ma l’attenzione minuziosa non si presta soltanto nelle fasi di progettazione e costruzione, infatti, Eurek utilizza specifiche buste antistatiche ESD con le quali proteggere le schede da possibili scariche elettrostatiche, che potrebbero compromettere la scheda, ed evitare che si depositino polveri una volta giunte al magazzino del cliente.
Per proteggere le schede durante il trasporto, Eurek ha ideato un particolare sistema a nido d’ape, costruito con cartone ondulato o cartoncino, che permette di suddividere il contenuto di una scatola e dedicare a ciascuna scheda uno spazio protetto.
A scelta del cliente, inoltre, è possibile effettuare un collaudo dei lotti di schede elettroniche prima che vengano spedite, seguendo procedure specifiche: ogni scheda viene controllata tramite un apposito simulatore, creato in fase di progettazione della stessa, che viene inserito nell’apparecchiatura di collaudo grazie alla quale viene simulato il funzionamento della scheda. In questo modo è possibile individuare tempestivamente eventuali problematiche e agire per risolverle. Nel caso di grandi lotti o schede particolari, Eurek personalizza il collaudo con tecnologie avanzate che si adattino perfettamente all’attività della scheda.
Qualunque sia l’esigenza per il tuo cuore elettronico, Eurek saprà costruire le schede elettroniche che lo completano. Contattaci e parleremo del tuo progetto davanti a un buon caffè