La costruzione della scheda elettronica è una fase fondamentale per il successo del tuo business: assicurarsi un dispositivo sicuro realizzato con cura nei minimi dettagli, ti consente di garantire al cliente finale un prodotto completo, funzionale e sicuro. Eurek questo lo sa bene e, per questo motivo, per ogni commissione mette a disposizione tutta l’esperienza maturata in anni di operatività nel settore dell’elettronica.
Ogni progetto viene seguito e gestito con estrema attenzione e cura al dettaglio: tutte le fasi necessarie per la creazione di ogni scheda elettronica vengono svolte seguendo precisi step, volti a garantire al cliente prodotti impeccabili.
La flessibilità di Eurek permette la costruzione di diverse schede elettroniche, sia progettate internamente, sia progettate da terzi. In questo modo, è possibile accogliere e soddisfare con successo qualsiasi richiesta ci venga effettuata. In questo articolo, puoi scoprire come avviene la creazione di schede elettroniche in Eurek.

La fase iniziale
Ogni scheda elettronica trova radici all’interno di un progetto iniziale: sia che venga commissionato direttamente ad Eurek, sia che sia stato realizzato da un progettista esterno, deve essere dettagliato e preciso. Al suo interno, infatti, si trovano informazioni essenziali per selezionare e ordinare i componenti necessari per la realizzazione della scheda, tra cui specifiche marche da impiegare o determinati elementi da montare sul prodotto. A questo punto si compila la BOM, in cui sono indicati i diversi componenti e le diverse posizioni in cui andranno collocati.
La distinta viene poi trasferita al magazzino, che provvede a preparare tutti gli elementi necessari per la costruzione della scheda. Una parola chiave che descrive Eurek è “organizzazione”, e la si può trovare alla base di ogni attività: anche il magazzino è disposto in maniera tale da poter trovare i componenti con rapidità, permettendo quindi di ridurre notevolmente i tempi di consegna del prodotto.
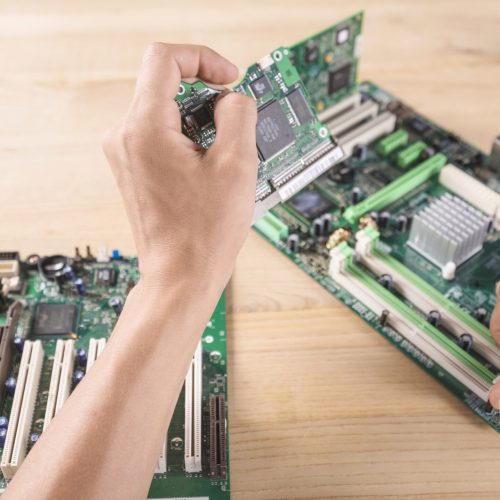
La costruzione della scheda
Una volta preparati i componenti necessari, si procede con il montaggio della scheda elettronica. Innanzitutto, è necessario avere chiaro quale tipo di montaggio si ha in programma. È importante distinguere i componenti SMT (Surface Mount Technology) dai componenti PTH (Pin Through Hole). Nel primo caso, la tecnologia impiegata è più avanzata, nella quale il montaggio avviene in maniera completamente automatizzata attraverso una macchina chiamata Pick&Place. Nel secondo caso, invece, il montaggio avviene eseguito principalmente in maniera manuale da operatrici specializzate.
La scelta del montaggio dipende soprattutto dalle caratteristiche che la scheda elettronica in questione possiede. Nella maggior parte dei casi, la scheda viene costruita attraverso il montaggio SMT, poiché è più rapido e preciso. Nonostante ciò, sia per scelta del progettista, sia a causa di elementi particolari posizionati sul circuito, si rivela ancora necessario il metodo PTH.
Prima di produrre la scheda elettronica in larga scala, si procede con la fase di prototipazione: questo passaggio permette di individuare preventivamente eventuali componenti non idonei per quel progetto, oppure particolari criticità del circuito stampato. In questo modo, si possono correggere subito eventuali imperfezioni e procedere più rapidamente con la successiva costruzione dell’intero lotto commissionato.
In seguito al montaggio degli elementi da parte della macchina Pick&Place nel caso di componenti SMT, o da parte degli operatori nel caso di componenti PTH, si procede con la saldatura. Da Eurek viene realizzata per mezzo di un forno vapour-phase che si basa su una tecnologia avanzata: conosciuto anche come processo di saldatura per condensazione, garantisce saldature di alta qualità assicurando che tutta la scheda raggiunga una temperatura uniforme, nonostante la presenza di elementi con caratteristiche molto diverse.
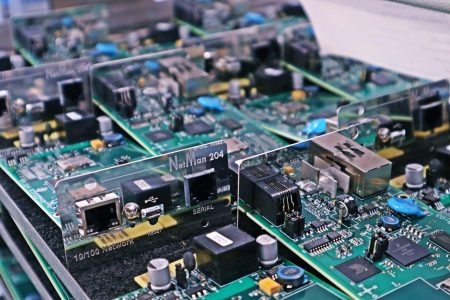
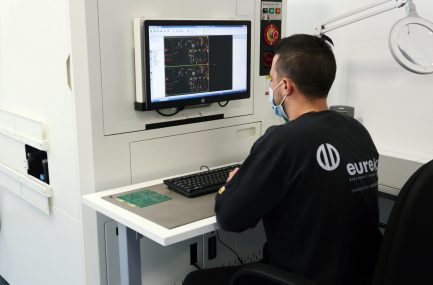
Ispezione ottica e imballaggio
Dopo aver correttamente saldato i componenti sul circuito stampato, la scheda elettronica viene controllata da una macchina dotata di controllo 3D chiamata AOI (Automatic Optical Inspection): tramite un programma realizzato appositamente per quella scheda, questa macchina verifica la presenza di stagno, il posizionamento dei componenti e la correttezza generale del lavoro eseguito.
Se il progetto lo prevede, si procede con il collaudo della scheda elettronica: attraverso un simulatore, si può verificare il corretto funzionamento della scheda sul prodotto finale. Così facendo, è possibile individuare eventuali criticità e procedere quanto prima alla loro correzione.
Terminata quest’ultima fase, infine, si conclude con l‘imballaggio dei prodotti. Ogni scheda elettronica viene accuratamente riposta in imballi di cartone, studiate per garantire un incastro ottimale, capace di tutelare i prodotti al meglio durante lo stoccaggio e il trasporto.
In conclusione
La costruzione della scheda elettronica è un processo delicato, che richiede l’intervento di operatori specializzati e competenti. Eurek si avvale di un team qualificato in ogni suo reparto, dal progetto della scheda fino al suo imballaggio, al fine di garantire ai suoi clienti un lavoro sicuro, realizzato con precisione in ogni suo dettaglio. Se ti occorre una scheda elettronica per la tua azienda, contattaci: siamo a tua disposizione per qualsiasi richiesta.